|
|
|
|
 |
|
|
|
|
 |
|
MOLECULAR
SIEVE
|
|
Adsorption on Molecular Sieve is characterized by a Langmuir-type isotherm, where the amount of a given compound adsorbed increases rapidly to a saturation value as
its pressure or concentration increases in the external bulk phase. Any further increase in pressure at constant temperature causes no further increase in the
amount adsorbed. With Molecular Sieves this equilibrium saturation value usually corresponds to a complete filling of the internal void volume with the adsorbate.
|
|
|
|
Molecular Sieve retain adsorbates by strong physical forces rather than by chemisorption. This means that when the adsorbed molecule is desorbed by the
application of heat or by displacement with another material, it leaves the crystal in the same chemical state as when it entered.
The external surface area of the Molecular Sieve crystal is available for adsorption of molecules of all sizes, whereas, the internal area is
available only to molecules small enough to enter the pores. The external area is only about 1 per cent of the total surface area. Materials which
are too large to be adsorbed internally will commonly be adsorbed externally to the extent of 0.2 to 1 weight per cent.
|
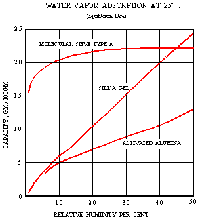 |
|
|
|
|
ADSORPTION
DIRECTION
|
Drying
Streams to Very Low Water
Contents
|
Drying by adsorption is used in industry because molecular sieve typically produces a drier liquid or gas than can be obtained by other commercial
methods. However, not all adsorbents can dry liquids to the same degree. Molecular sieve is outstanding in their ability to produce low
effluent water concentration. They are the ideal adsorbent to use wherever extremely dry streams are required. Water concentrations as
low as 35 parts per billion are obtainable in dynamic drying service over a wide range of operating conditions.
|
|
Drying
and Purifying Streams In
One Step
|
By selection of the molecular sieve type and the proper operating conditions, it is possible to remove other impurities from the stream along
with water. As has already been pointed out, molecular sieve adsorb water more strongly than any other material. As a result, the adsorbed
water concentrates initially at the inlet end of the bed where it displaces the other impurities that have been previously adsorbed. These
desorbed impurities are then re-adsorbed farther down the column.
As displacement continues, the desorbed impurities will begin to appear in the effluent stream. In normal drying operations this displacement
is allowed to continue until little adsorbate, other than water, is left on the bed. However, molecular sieve is possible to design and
operate a molecular sieve adsorption system in such a manner that the other impurities are retained on the adsorbent, instead of allowing
them to re-enter the purified stream. molecular sieve is necessary, of course, to provide sufficient bed to contain the impurities in addition
to the water. Isotherms showing equilibrium loading for some of the more common impurities encountered in purification processes are shown
in above figures.
|
|
Drying
Without Altering Stream
Composition
|
In some drying operations molecular sieve is not unusual to find that other components of the feed are adsorbed in addition to water. Where
product composition is critical, as is the case with many chemical process stream, co-adsorption presents a serious problem. In fact, in
some instances adsorption has been ruled out completely and another method of drying adopted because molecular sieve was impossible or
impartial to control co-adsorption. This need not be the case if molecular sieve is used.
The co-adsorption problem can be solved easily by selecting a molecular sieve type with a critical pore diameter small enough to prevent
all stream components except water from being admitted to the active inner surfaces of the adsorption cavities. This prevents the co-adsorption
of materials other than water - including polar and unsaturated components-while providing maximum capacity for water and effluent
water concentrations of one to ten parts per million.
Another factor bearing on the elimination of co-adsorption is the extremely high adsorptive attraction for water possessed by molecular
sieve. This affinity is so strong that water will normally displace any other material that is already adsorbed on them. Also, molecular
sieve is possible to enhance this normal selectivity by raising the temperature of the bed. The rate of adsorption will be somewhat
reduced if the water has to displace another material before molecular sieve can be adsorbed. Despite this, molecular sieve still offer
a great improvement in performance over other adsorption systems.
|
|
Drying
Streams at High Temperature
|
Molecular sieve is the only adsorbents that can dry streams effectively at high temperatures. The isobars plotted in the accompanying graph
illustrate this type of performance. At 200oF (93oC) and above, they have better than 13 weight percent capacity. Even at 400oF (204oC.),
they still have a capacity of 3 weight percent. By comparison, the equilibrium capacity of alumina and silica gel type desiccants decreases
rapidly as soon as the temperature rises above 75 or 80oF (25oC). At 300oF (149oC.), both of these desiccants have lost their capacity
for water, while molecular sieve still have the ability to adsorb some water at temperatures over 600oF (316oC.)
|
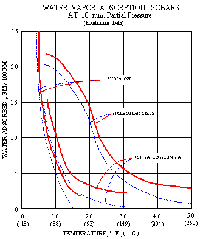 |
The isobars which appear as solid lines assume the use of completely regenerated adsorbents. The capacity is lowered by any residual
water left on the adsorbent; this factor is especially important in high temperature drying. The effect of 2 percent residual
water at the start of adsorption is shown by the dotted line isobars. In some applications, this amount of water can completely
consume the adsorption whereas this or even greater amounts of residual water have relatively little effect on the capacity
of molecular sieve.
|
|
|
|
|
|
|
|
|
STRUCTURE
ANALASIS
|
Formula
|
Na86 [ ( AIO
2) 86 (Si92) 106 ] H
2O.
|
|
Description
|
White ball or cylinder type, high specific surface area, generally used as an adsorbent.
|
|
Preparation
|
Mixed raw material according the mole ration:
|
Al
2O
3
|
: 10%
|
SiO
2
|
: 36.60%
|
NaOH
|
: 48.10%
|
H
2O
|
: 1.80%
|
|
Mixture stirred under 102 +/- 2oC, Crystallized and shaped, activated.
|
|
|
Uses
|
For general gas drying, air plant feed purification (simultaneous removal of H
2O and CO
2) and liquid hydrocarbon and natural gas sweetening (H
2S and merchantman removal).
|
|
|
|
|
|
|
|
13X
MOLECULAR SIEVE
|
Description
|
Molsiv adsorbent type 13X, the sodium form of the type X crystal structure, is an alkali metal alumino-silicate. Type 13X will adsorb molecules
with critical diameters up to 10 angstroms.
|
|
Applications
|
Type 13X is used commercially for general gas drying, air plant feed purification (simultancous removal of H2O and CO2) and liquid hydrocarbon
and natural gas sweetening (H2S and mercaptan removal).
All molecules which can be adsorbed on Molecular Sieve type 3A, 4A, and 5A can be sdsorbed on type 13X. In addition, type 13X can
adsorb molecuies of larger criticai diameters, such as aromatics and branched-chain hydrocarbons.
|
|
Chemical
Formula
|
Na36 [(AlO
2) wxy (SiO
2) wxy] X H
2O
|
|
Regeneration
|
Molsiv adsorbent type 13X can be regenerated for re-use by purging or evacuating at elevated temperatures. The degree of regeneration
(water removal) is dependent on the temperature and humidity of the purge gas.
|
Type Properties
|
1/16" Pellets
|
1/8" Pellets
|
Powder
|
8x12 Beads
|
4x8 Beads
|
Nominal Pore Diameter
|
10 Angstroms
|
10 Angstroms
|
10 Angstroms
|
10 Angstroms
|
10 Angstroms
|
Bulk Density
|
38 lbs/cu ft
|
38 lbs/cu ft
|
- - -
|
40 lbs/cu ft
|
40 lbs/cu ft
|
Hydrated Wet Density
|
- - -
|
- - -
|
1.95 g/cc
|
- - -
|
- - -
|
Activated Dry Density
|
- - -
|
- - -
|
1.53 g/cc
|
- - -
|
- - -
|
Particle Diameter
|
0.0575 in.
to 0.0775 in.
|
0.115 in.
to 0.135 in.
|
< 10 microns*
|
100%thru-8 <5%thru-12
|
100%thru-4 <5%thru-8
|
Crush Strength
|
7 lbs
|
14 lbs
|
- - -
|
4
|
15
|
Crystal Structure
|
- - -
|
- - -
|
Cubic
|
- - -
|
- - -
|
|
|
|
Type Properties
|
1/16" Pellets
|
1/8" Pellets
|
Powder
|
8x12 Beads
|
4x8 Beads
|
Heat of Adsorption (max)
|
1800 btu/lb H2O
|
1800 btu/lb H2O
|
1800 btu/lb H2O
|
1800 btu/lb H2O
|
1800 btu/lb H2O
|
Equilibrium H2O
Capacity**
|
24% wt
|
24% wt
|
24% wt
|
24% wt
|
24% wt
|
Water Content (as shipped)
|
< 1.5% wt
|
< 1.5% wt
|
< 1.5% wt
|
< 1.5% wt
|
< 1.5% wt
|
Molecules Adsorbed
|
Molecules with an effective diameter <10 angstroms.
|
Molecules Excluded
|
Molecules with an effective diameter >10 angstroms. E.g., (C4F9)N
|
|
*
|
Agglomerate panicle size. Average crystal size is 1.0 to 4.5 microns.
|
**
|
Lbs H2O/100 lbs activated adsorbent at 17.5 mm Hg 25oC.
|
|
|
|
|
|
|
|
|
|
13X
MOLECULAR SIEVE TECHNICAL DATA
SHEET
|
Nominal Pore Size
|
- - - - - - - - - - - - - - - - - - - - - -
|
10 Angstoms
|
|
Type of Crystal Structure
|
- - - - - - - - - - - - - -
|
Body Center Cubic
|
|
Equilibrium Water Capacity @ 25°C
|
- - - -
|
@ 10% RH 19% @ 50% RH 22%
|
|
Bulk Density
|
- - - - - - - - - - - - - - - - - - - - - - - - - - -
|
40.6 / 0.5
|
|
Crush Strength
|
- - - - - - - - - - - - - - - - - - - - - - - - -
|
7.7 lbs
|
|
Heat of Adsorption (max.)
|
- - - - - - - - - - - - -
|
1800 BTU / 16 H
2O
|
|
PH (Slurry)
|
- - - - - - - - - - - - - - - - - - - - - - - - - - - - -
|
11 / 1
|
|
Loss on Ignition
|
- - - - - - - - - - - - - - - - - - - - - - - -
|
2.5% Max.
|
|
|
|
Applications:
|
Type 13X is used commercially for general gas drying, air plant feed purification (simultaneous removal of H2O and CO2) and liquid hydrocarbon
and natural gas sweetening (H2S and mercapstan removal). All molecules which can be adsorbed on molecular sieves 3A, 4A and 5A can be adsorbed
on type 13X. In addition, type 13X can adsorb molecules of larger critical diameters, such as aromatics and branches-chain hydrocarbons
|
|
|
|
|
|
|
 |
 |
|
SILICA
GEL DESICCANT GRADE PRODUCT DETILS AND
SPECIFICATIONS
|
|
Non-Indicating (White) Type: This has high absorption efficiency. It absorbs water and all condensable vapors whose boiling point is above 10℃. It does not contain
any indicator so it is not easy to ascertain whether it has completely moisturized.
The above product is free from foreign impurities such as Chlorides, Sulphates and organic matter and have high absorption efficiency.
Absorption efficiency increases under higher humidity, higher pressure and lower temperature. It can be regenerated by first keeping in sun light or heating
to a temperature of 150℃. The product should not be heated to temperatures above 250℃ as at this stage Silica Gel loses all of it's water content, leading
to a complete loss of all the properties of absorption.
|
|
|
|
SN0316
SPECIFICATIONS
|
|
Absorption efficiency: Above 25% under 50% R.H. and 20℃ temperature: Above 65% under 100% R.H. and 20℃ temperature.
Combined Water: Maximum 6% (Loss or drying at 150℃).
Chloride (as NaCl): Less than 0.05%.
|
|
|
|
SN0316
SPECIFICATIONS
|
|
Sulphate (as Na2 So4): Less than 0.25% Organic Matter (as NH3): Less than 0.001%. PH: Between 6 to 8. Cobalt Chloride: 1 to 1.5% (in Indicating type Blue). Friability and dust: Less than 0.05%. Average purity: 99.80 or more % Silica (SiO2) or dry basis.
|
|
|
|
PHYSICAL
CONSTRAINTS
|
|
Pore Volume: 1.2 to 1.3 cc/gm Pore Diameter: Average 140 to 150 Angstrom Units.
Surface Area: 500 to 700 square meters per gm. Average Porosity: 60 to 65% Thermal Conductivity: 1 BTU/sq ft / hr / F / in. Sp Heat: 0.2 to 0.22
BTU / lb / F Specific Gravity: 2.10 to 2.30 Hardness: 5 on Moh Mineralogical Scale. Oil absorption: 1.6 g/g Percentage of Fe / other impurities:
Nil.
Capacity to absorb: Moisture from air, any condensable vapours, oil. Acetylene and other hydrocarbons from liquid oxygen. Re-activation temperature: 150℃
|
|
|
|
THE
CHARACTERISTICS AND SAFETY PERFOMANCE
|
|
Silica Gel is a kind of highly active adsorption material. It is usually formulated by sodium silicate and sulphuric acid reaction and through a series of after treatment
processes such as aging, pickling, etc. Silica Gel is amorphous substance. Its chemical molecular formula is SiO2, nH2O. It is insoluble in water and any other
solvent. It is nontoxic, nonodor and chemically stable. Except ofr alkali and hydrofluoric acid, it does not react with any other substance. Owing to their different
manufacturing methods, the various types of silica gels are formulated with different pore structures. Thanks to its unique chemical composition and physical structure.
Silica Gel possesses a number of characteristics with which other similar materials are incomparable, such as high adsorption feature, stable thermal performance,
stable physical property and relatively high mechanical strength etc.
According to the different pore diameters of Silica Gel, they are categorized into large pore Silica Gel, macro-pored Silica Gel, B type Silica Gel and fine-pore
Silica Gel. Owing to their different pore structures, their adsorptive performances are variable. Under the circumstance where there is a high relative humidity,
macro-pored Silica Gel (c type) has a relatively high adsorption capacity. Whereas, under the circumstance where there is a low relative humidity, Ting-pored
Silica Gel (A type) has a higher adsorption capacity than macro-pored and fine-pored Silica Gel. The pore structure of Silica Gel type B lies between macro-pored
and fine-pored Silica Gel, so its adsorption amount is also between those of macro-pored and fine-pored Silica Gel. Large pored Silica Gel is usually used
as catalyst carrier, matting agent and toothpaste abrasive, etc. Therefore, the appropriate type is to be selected according to your specific field of application.
|
|
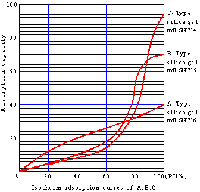 |
|
|
|
|
|
|
|
|
|
ACTIVATED
ALUMINA PRODUCT DETILS AND SPECIFICATIONS
|
|
TECHNICAL
DATA: F-200
|
|
Activated Alumina is an aluminum oxide which is highly porous and exhibits tremendous surface area. Activated Alumina is resistant to thermal shock and abrasion and
will not shrink, swell, soften nor disintegrate when immersed in water.
Masda features F-200 Activated Alumina. F-200 is known for its uniform ball size, high crush strength, low abrasion, high pressure drop and adsorption capacity.
|
|
|
|
PARTICLE
SHAPE AND SIZE
|
|
F-200 is available in very smooth, uniform balls of 1/8" (3.2 mm), 3/16" (4.8 mm) or 1/4" (6.4 mm). The uniformity of ball size prevents channeling
of the gas flow and minimizes pressure drop.
|
|
|
|
PRODUCT
APPLICATIONS
|
|
Drying - Nearly all gases and liquids can be dried with F-200. Due to the high surface area (350 sq. meters / gram), F-200 is an effective adsorbent in such gases
as Acetylene, Oxygen, Methane and Oxygen along with fluids such as Benzene, Freon, Hydraulic Oils, Kerosene, transformer and vegetable oils.
|
|
|
|
Acid Removal - Transformer oils, lubricating oils and refrigerants all form degradation acids upon use. F-200 Activated Alumina will remove these corrosive acids thus
protecting valuable equipment.
|
|
|
|
PHYSICAL
PROTOTIES
|
|
Size: O 3-5 mm, O 4-6 mm, O 5-7 mm, O 3 X 3-8 mm small ball with grain size of 30-200 mesh.
A white or slight-red particle, ball-shaped or roll-shaped, insoluble in water and organic solvent, soluble in strong acids and alkalis, odourless, tasteless,
non-toxic. After adsorbing moisture in air, it does not expand and crack, and keeps its original shape. It is adsorptive with Nox, F2, as and other gases.
Widely used as catalyst for recovering sulfur in petrochemical industry, excellent defluorinating agent for drinking water, defluorinating agent for recycling
alkyl-hydrocarbon in alky benzene production, reclaiming agent for deacidic in transformer oil, dearsenic agent in acid industry, adsorbent in the production
of hydrogen peroxide solution, catalyst for polyhydro-ammonia by substituting Silica Gel with ball-shaped product, desiccator and purifying agent for different
kinds of gases and liquids. In recent years, we have developed two types of new products - LS811 and LS-931 according to the
market requirement. With reasonable structure and higher application performance, the products are mainly used as catalyst for oil production and Klaus
sulfur recycling equipment full of acidic gas, featuring high transfer efficiency, ling life, good effect of desulphuration for waste gas, and good performance
for anti-sulfate toxic.
|
|
|
|
|
|
TECHNICAL
DATA SHEET SPHERES F-200
|
|
TYPICAL
PROPERTIES
|
CHEMICAL
|
Al203
|
- - - - - - - - - - - - - - - - - - - - - - - - - - - - - - - - - -
|
93.01%
|
|
Sio2
|
- - - - - - - - - - - - - - - - - - - - - - - - - - - - - - - - - -
|
02%
|
|
Fe2O3
|
- - - - - - - - - - - - - - - - - - - - - - - - - - - - - - - - - -
|
02%
|
|
Na2O
|
- - - - - - - - - - - - - - - - - - - - - - - - - - - - - - - - - -
|
30%
|
|
LOI
|
- - - - - - - - - - - - - - - - - - - - - - - - - - - - - - - - - -
|
6.50%
|
|
|
PHYSICAL
|
TOTAL PORE VOLUME
|
- - - - - - - - - - - - - - - - - - - - - - - - - - - - - - -
|
0.5 cc/gram
|
|
|
SURFACE
|
AREA
|
- - - - - - - - - - - - - - - - - - - - - - - - - - - - - - - - - - - - - - - - - - - -
|
350 m
2 / gram
|
|
STATIC ADSORPTION
|
@ 60% RH- - - - - - - - - - - - - - - - - - - - - - - -
|
22%
|
@ 100% RH- - - - - - - - - - - - - - - - - - - - - - -
|
43%
|
ABRASION LOSS
|
- - - - - - - - - - - - - - - - - - - - - - - - - - - - - - - - - - - - - - - - - -
|
0.1%
|
|
BULK DENSITY
|
- - - - - - - - - - - - - - - - - - - - - - - - - - - -
|
48 lbs / ft3 / 0.77g / cc
|
|
|
|
APPLICATIONS
|
Desiccant in air, gas and refrigerant drying. F-200 is physically strong and resistant to attrition and abrasion. It is suitable for pneumatic handling.
It exhibits high density and adsorptive capacity, thereby providing high volumetric capacity.
|
|
|
|
TYPICAL
PROPERTIES
|
|
CHEMICAL
COMPOSITION
|
|
SiO2
|
< = 0.06
|
Fe2O3%
|
< = 0.03
|
Na2O%
|
< = 0.50
|
BET-surface
|
300 + -20 m2/g
|
Pore-volume
|
0.4 + -0.02 ml/g
|
Moisture adsorption
|
> = 50
|
Static water-adsorption
|
> 20.0%
|
Specific wear ability
|
< 0.05%
|
Bulk density
|
0.7 + -0.02 kg/L
|
Crushing strength
|
Min. 120 N
|
|
|
|
|
|
|
|
|
|
|
|
|
|